3 Reasons Machine Vision is Important
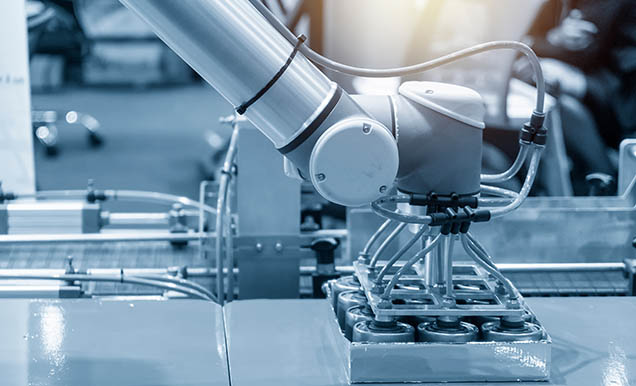
When thinking of health, safety and controlled environments in product manufacturing, one focus area would be the food and drink industry. Consistent quality in both the product and its packaging is the goal, and machine vision is increasingly being used to achieve this. Machine vision systems for inspection don’t just scan for defects, they ensure products meet the set standards of global food associations by looking for contaminants, they check for any functional flaws within the packaging structure, and look for multiple irregularities set within the programming parameters.
People are still essential in identifying defects, but this human intervention has evolved and roles have expanded from not just pickers and packers (which are still needed) but now include programmers and data analysts. Identification of inconsistencies at scale now uses automation to achieve both consistency and at speed. Here's 3 ways in which is does that:
1. Quality control
Vision-based quality control automation processes can assist with portioning items equally. For example, in the case of a pack of chewing gum the machine can make sure there are an equal number of sticks/chews in each pack and that there are no discrepancies.
Not only that, but machine vision systems ensure uniform structural integrity - important for keeping the product itself compliant but also for the sale and marketing side of the product. To continue the chewing gum example, any discrepancies in the number of units per pack would not only be sub-standard for the customer but could affect structural integrity of any bulk display.
2. It's not just a box… it’s a brand
A product is not a stand-alone object; it sits with others of the same brand or same type on a shelf as part of a collection that needs to be visually appealing to the consumer - especially if it’s a new brand in a congested market. Whether a differentiator or chameleon product (attempting to be as close as possible to a brand leader) we live in a visual society where a description or technical specification are no longer enough to seal the deal. This is where machine vision systems can catch defects in real-time and remove those items that do not conform to the brand guidelines so protecting the brand’s reputation for quality. Ultimately it makes operations more efficient and reduces waste by pulling elements in time to be remedied.
3. Clarity and consistency in labelling
Mislabelling, or simply a lack of information on printed products, can cause a multitude of issues, both from a trading compliance point of view and details for consumer safety. Without the proper information products might face being recalled which leads to financial loss, not only to the manufacturer but throughout the supply chain, as well as damage to brand reputation both direct and indirectly. When food and drink products suffer this fate, such as including allergens without making their inclusion clearly identifiable, the associated dangers can make global news. That’s why machine vison systems can be crucial to avoiding such scenarios by checking every unit before it leaves the manufacturing plant door.
So what’s the future of machine vision systems?
Although we’re talking about the product, packaging and labelling as discrete items here, automation and machine vision help merge these factors to give from source to shelf - that same full tracking that is as vital in the food and beverage industry as other markets.
Technology has always been the key driver in improvement: from better sensors, accuracy and speed in frame grabbers and cable sizing/weight, and clarity in cameras, to hardware/software upgrades and the ability to communicate with other systems. Machine learning parameters, system communication, and the advancements in artificial intelligence are now the technology that are delivering full traceability, quality control, and automation improvements in the food industry and beyond.