Cable specification: The cost of getting it wrong
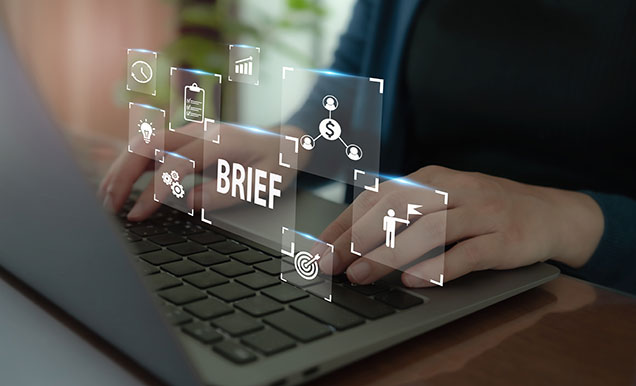
The proper specification of cables has always been crucial in electrical installations, with implications that extend far beyond operational efficiency. As unplanned downtime become costlier than ever, getting things right has never been more important.
To help you avoid common cable pitfalls, we’ve compiled a list of areas where cable specifications can miss the mark, along with the key considerations and best practice advice you need to select the right cable for your project.
Where can cable specifications go wrong?
It goes without saying: cable specification is a complex process. Ensuring your cable meets the needs of your project can involve a myriad of considerations, spanning performance, safety and reliability.
It’s no wonder that mistakes occur. Let’s simplify your decision-making. Here are four of the most common issues that arise from incorrect specifications, so you can look out for them in your next project.
- Incorrect power load calculations
An inaccurate calculation of the power load can lead to under- or over-specification, impacting energy costs and system efficiency.
- Incompatibility with installation designs
A cable that isn’t well suited to its installation can cause complications during the build phase. For example, if a rigid cable is supplied for an installation with tight bends in the design, this could necessitate larger earthworks and complicate cable routing to bend it into place. A more flexible cable may be better suited to the installation.
- A lack of consideration for environmental factors
Whether it’s inadequate armouring for mechanical protection, a lack of UV resistance, water protection, or lacking chemical, oil and grease resistance, they can damage the cable sheath and cause performance and safety issues that lead to premature failure.
- Not meeting the regulatory or legislative requirements
A cable that meets all the requirements of the above three points is still non-compliant if it doesn’t meet the regulatory requirements. For fixed wiring, whether it’s the CPR classification it holds or meeting national building code standards, assuring compliance is essential. The same applies when connecting equipment – is it compliant with manufacturer guidelines (or risk voiding any warranties).
What are the implications of incorrect cable specification?
These errors can have major consequences for your cable projects, including (but not limited to):
Safety hazards
At worst, cable failures as a result of incorrect specification can cause short circuits, which may lead to fire or electrical shock. This could result in severe accidents and injuries – not to mention the associated costs associated with repair and replacement, the legal liabilities, and the risk of damage to reputation.
Inefficient operations
Inefficient operations can have a knock-on effect on connected equipment, potentially causing issues and damage across entire networks. While it’s crucial to bear in mind under-engineering with its risk of overheating, you also don’t want to over-engineer as larger cables take more space (when it is often at a premium onsite) and weigh more (perhaps requiring changes to containment and routing).
Increased costs
Specifying the wrong cable – especially when this results in buying more expensive cable than is needed – is not just about the additional upfront costs. It can lead to increased energy costs, impacting the overall operational expenses. The wrong specification and the inefficient operations that brings can also mean more maintenance and higher replacement costs, adding to the total cost of ownership.
Understanding cable materials
So, how can you ensure your cable is well-suited to its specification? Where should you start when making a specification decision? The answer is simple: it’s all in the cable materials.
A thorough understanding of different cable materials and their properties enables more informed decision-making during specification, leading to cables that are better suited to the application's needs – be that performance, safety, durability or cost-effectiveness.
Cable sheath type
The cable sheath is the primary layer of protection against the environmental challenges a cable will face during its lifespan. A number of different types are available – PVC, LSZH, Rubber, MDPE and more – with each offering their own unique properties. Finding the balance and ‘best-fit’ compromise to offer the characteristics you need is the aim.
For guidance on which is best suited to your project, check out our FAQ page, where we provide the key benefits and drawbacks of several different sheathing materials.
Armoured or unarmoured?
Armoured cables offer additional protection against physical damage, which can be vital in environments where cables are exposed to mechanical stress, buried directly in the ground, or at risk of penetrating damage, such as in industrial settings. On the other hand, non-armoured cables are less rigid and easier to install (and terminate), and mechanical protection can potentially be provided for in the choice of containment.
Choosing the appropriate type of cable (compliant with any national building and construction regulations) ensures that it can withstand the specific conditions of its installation site, enhancing both the safety and reliability of the overall installation.
Conductor size
The cable conductor size and the choice of conductor material determine its ability to deliver the current carrying capacity required - critical for maintaining system efficiency and safety. Factors such as voltage drop must also be considered, taking into account the distance the power is to be transmitted (voltage loss over distance), reducing the performance of connected equipment. Properly sizing the conductor ensures that the electrical system will operate within its intended parameters, minimising energy losses and prolonging the lifespan of the cable.
Our Cable size calculator (for Low Voltage Cables) for compliance with BS7671 or IEC 60364-5-52 can help guide you.
Insulation
The insulation material of a cable determines its ability to withstand operational performance stresses, ensuring longevity and reliable performance. The operational parameters (as well as any applicable standards) will guide as to which is best suited for your installation. Cross-linked Polyethylene (XLPE) is now the most common insulation material for both Low and Medium Voltage cables as it offers excellent thermal resistance and allows for a maximum conductor operating temperature of +90oC. EPR (Ethylene Propylene Rubber) is also specified in some MV cables, whilst XLOHLS (Cross-linked low smoke zero halogen) and PVC and can be found on some low voltage power and instrumentation cables although the latter has a maximum conductor operating temperature of +70oC.
How Eland Cables can help
If you're still unsure about selecting the right cable for your project or need additional support on the compliance side, Eland Cables’ technical team can help guide you to a solution. Our cables are also rigorously tested in our ISO/IEC 17025 & IECEE CBTL accredited laboratory to assure quality and compliance.
Don't leave your cable specification to chance. Reach out to Eland Cables today and let us help you achieve optimal performance for your electrical installations.