MV Cables: The Lowdown
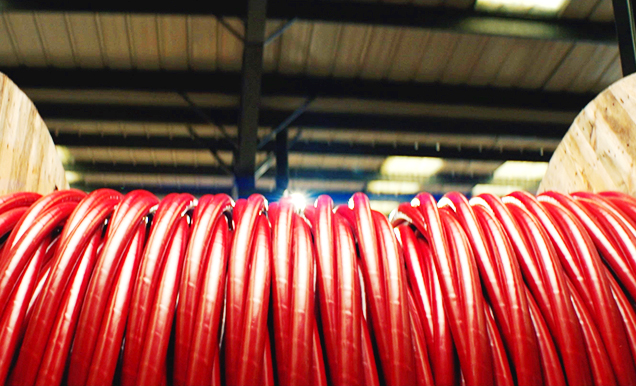
Did you know that there are several definitions within the cable world for classifying Medium Voltage? Perhaps the most commonly referenced is the International Electrotechnical Commission’s voltage standard IEC 60038 where medium voltage (MV) is a nominal voltage between 1kV and 35kV. But within that range there are a wide range of cable types, applications, materials and properties, making understanding these different factors essential in determining which MV cable is best suited for any installation.
What makes a Medium Voltage Cables?
The construction of an MV cable will be heavily influenced by its installation environment and intended function, but it can start from as few as 6 layers (3 of which are applied in a triple extrusion process) to upwards of 10 layers.
- Conductor: Carries electric current, typically made of copper or aluminium.
- (Optional) Conductor Waterblocking: using swellable powders or yarns for protection against water ingress.
- Conductor Screen: A semi-conductive layer which guarantees a uniform electric field in the interface between the insulation and the conductor, as well as preventing any electric field concentration/spikes.
- Insulation: Critical for MV cables, made of XLPE (cross-linked polythene), HEPR (hard grade ethylene propylene rubber) or EPR (ethylene propylene rubber) to withstand high electric fields. Thickness increases with voltage.
- Insulation Screen: A second semi-conductive layer, which performs a similar function to the conductor screen. Together with the conductor screen and insulation materials itself, these are normally applied in a triple extrusion.
- (Optional) Longitudinal waterblocking: A measure of protection against water ingress, using semi-conductive tapes or swellable powders underneath and above the metallic core screen to prevent propagation through the length of the cable.
- Metallic Core Screen: Covers insulation, typically a concentric layer of helically applied copper wires and/or copper tape for electromagnetic compatibility.
- (Optional) Inner Sheath: Applied where Armour is also applied for extra protection, preventing the layers beneath the armour from being damaged by the armour itself.
- (Optional) Armour: Aluminium wires for Single cores, steel wires for multicores – may also be tapes (flat, double layered, or corrugated) for mechanical protection. Braided screens may also be used for more flexible mechanical protection or to counter torsional stresses where linked to dynamic equipment connections
- (Optional) data or pilot cores: Mainly seen in cables for heavy industry such as mining, the addition of data/fibre cores to provide monitoring whilst pilot cores are for monitoring earthing continuity protection.
- (Optional) Radial waterblocking: Provides additional water protection against sheath damage via an Aluminium/PET (polyester) Tape with the aluminium side tightly bonded to the outer sheath.
- Outer Sheath: Provides the environmental barrier. Usually PVC, MDPE, Rubber, or LSZH materials. Depending on the material, it may offer flame retardance, UV resistance, and resistance against oils & greases, water, chemicals, and abrasions.
What types of MV cables are there? How do I choose the right one for my project?
The most appropriate cable is the one that best matches the performance demands, installation design and will withstand the environmental challenges it will be subject to during its lifetime of operations.
MV cables can be largely separated into two categories – for grid power distribution or for powering heavy-duty equipment. As a distribution cable, MV is generally employed to mitigate electrical losses when transporting electricity over a fixed distance. The further the distance the higher the voltage needed. This applies whether it’s for a public power grid or for specific applications like a railway network.
For static and dynamic equipment such as used in the mining industry, and in ports and quarries, it may be that an MV connection is also required, rather than it being stepped down to low voltage. Cables for dynamic applications may also require additional characteristics such as increased flexibility, resistance to oils and chemicals, and protect against torsional stresses if subject to reeling.
Below, we've highlighted some examples of commonly specified cables for different voltage ratings, along with some of the properties that make them suitable for different types of projects.
Grid Power and Mains Power Distribution
Medium Voltage cables of 10kV and 11kV are used in power distribution networks which span shorter distances between substations and local transformer stations. They are also used for power distribution in industrial complexes, manufacturing plants and large commercial buildings. 10 kV is a common distribution voltage across the synchronous grid of continental Europe. Supplying over 400 million customers in 24 countries, it’s the largest MV grid of its kind in the world.
Example cable – N2XS(FL)2Y 6/10kV – Abrasion and tear resistant MDPE sheath. Waterblocking layers to prevent ingress or where laid in waterlogged ducts. Copper conductors to minimise space needed.
11kV is the voltage that the UK uses for shorter distances within the power distribution networks which go to the final step down transformer. The Distribution Network Operators use their own specification variation on BS7870-4.10, whilst the armoured BS6622 PVC and BS7835 LSZH are also sometimes specified for direct burial applications.
Example cable: BS7870-4.10 triplex 6.35/11kV – Copper or Aluminium depending on the location parameters – aluminium triplex is lighter so easier to pull in but requires a larger cross-sectional area size to match current carrying capacity.
Increasingly 10kV and 11kV cables are being installed directly into high-rise buildings to mitigate the Voltage drop issues. LV cables would require multiple runs of large conductors to eliminate these problems so instead MV cables run up the building risers to individual floors, with transformers stepping down to mains voltage for floor distribution. These cables are LSZH as they are part of the fixed wiring within buildings and construction so must be compliant with the Construction Products Regulation (CPR).
Example cable: BS7835 6.35/11kV – Low Smoke Zero Halogen sheathing provides protection in the event of fire, aiding evacuation and fire fighting efforts. Typically Copper conductors as facing space limitations.
20kV, 30kV (European) and 33kV (British) are at the higher end of the Medium Voltage bracket used for power distribution. These are typically over longer distances – but still often buried in cable ducts or direct in the ground (rather than on overhead line via pylons which is more commonly for high voltage installations). They will provide the connection from transmission substations to utility substations where it is advantageous to minimise resistive losses, as well as direct to power-intensive users such as large factories and mines.
Example cable: NA2XS(FL)2Y 18/30kV – Aluminium conductors as no space constraints.
Powering industry
As highlighted, in European installations and networks, mains power distribution cables with a voltage rating of 20kV are common. In industrial settings, they also connect applications such as generators and power heavy-duty equipment.
Example cable N2XSH HD620: LSZH sheathing is suited to internal/external applications. HD620 compliance (subsections dependent on geographic location) sets different constructional requirements.
Heavy industry sees Medium Voltage cables used directly for transmitting power at higher voltage levels within mining operations. These cables typically range from 5kV to 35kV and are utilized in applications such as powering motors, pumps, and other heavy machinery. Similarly, these types of cables are used in large scale material handling applications such as container handling gantries and ship loading cranes.
Example cable (N)TSCGEWÖU: The flexible Class 5 stranded tinned conductor and the robust but flexible Rubber insulation and sheathing layers are combined with an anti-torsion braid to support trailing and material handling applications.
Powering transport networks
Railway networks across Europe use different medium voltage ratings to provide trackside and overhead line power. In the UK it’s 19/33kV and 25/44kV for three-phase AC electrical power to traction substations on electrified lines, whilst France use a combination of 1.5kV (low voltage) and 25/44kV, the 25/44kV is also the voltage of Portugal and much of Eastern Europe’s rail networks. Germany, Switzerland and Austria operate on 8.7/15kV.
Example cable NR/PS/ELP/00008 25/44kV: The graphite coating acts as a semi-conductive layer allowing for post-installation sheath testing to confirm the cable has not been damaged whilst being pulled in.
Eland Cables: Your MV cable partner
We understand the importance of selecting the best-fit MV cable for your project along with choosing a supplier you can trust. Our technical and industry experts are on hand to support your project through specification and delivery, calling on an extensive stockholding or utilising some of the shortest manufacturing lead times in the industry.
All of our Medium Voltage cables are quality and compliance assured, having been put through additional rigorous testing by our industry-leading Cable Lab under the BSI Cable Testing Verification Kitemark. It provides extra peace of mind that your cables will meet the demands placed on them, throughout their operational lifespan.
Working on an MV project? Speak to our team today to learn more about how we can help – from sustainability measures to project management support.
Eland Cables: Trusted by Industry